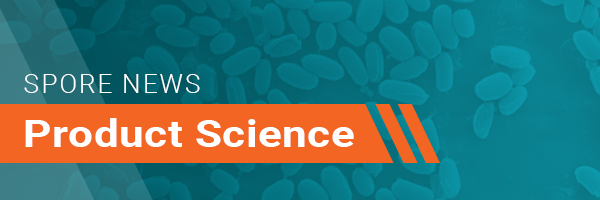
How Much Variation Should You Allow When You Specify a D-value?
By John R. Gillis, Ph.D. and updated by Mesa staff
Today we had a customer who requested a biological indicator (BI) with a D121-value of 2.0 minutes. The customer stated that a BI with a D121 of 2.1 minutes would not meet his purchase specification, which stated a D-value of 2.0 minutes.
There is a lot of misunderstanding regarding D-values. Here are some facts that may help to clarify this issue.
- ISO has standards for resistometers. These are very specialized test instruments used to perform D-value testing.
- The temperature control tolerance required is ±0.5°C.
- Spores die at very predictable rates. The higher the temperature, the faster they will die.
- The D-value is defined as the time that it takes at a specified set of conditions to reduce the spore population by 90% or one log.
- The z-value is the temperature change necessary to alter the D-value by one log.
- A common z-value for steam processes is 10°C.
All that said, let’s look at the capabilities of resistometer performance. A resistometer that controls ± 0.5°C from its set point, come-up to sterilizing conditions within 10 seconds, and come-down from sterilizing conditions within 10 seconds meet all current regulatory standards. What does a temperature control condition of ± 0.5°C mean to the potential D-value variance? Keep in mind that this is the most sophisticated test equipment available. If spore performance is as predictable as the D-value and z-value mathematical equations imply, then we can use those biological values to demonstrate the different lethality rates based on equipment variances of temperature delivered to resistometers.
Let’s use the example:
The D-value calculated at 121°C in a resistometer operating at a theoretical temperature variance of ± 0.0°C is 2.0 minutes. When the temperature is at - 0.5°C (lower acceptable limit), the calculated D-value increases to 2.2 minutes using a z-value of 10°C. Conversely, when the resistometer operates at + 0.5°C (higher acceptable limit), using the same calculation with the z-value, the D-value decreases to 1.8 minutes. Keep in mind that the spores have not changed, only the operating conditions within the resistometer have changed, and these parameter variances are those required and allowed in the regulations.
Therefore, if all test conditions are met for those spores, the expected and predictable D- value variance is 2.0 ± 0.2 minutes. That means any D-value expressed between 1.8 minutes and 2.2 minutes is exactly the same predictor of spore performance based on a 121.0 ± 0.5°C cycle. These spores are responding only to the acceptable variances allowed for control of resistometer test equipment.
Mesa performed a study using our resistometer, which has a much narrower temperature variance than allowed by the standard. We normally expect a temperature variance of ±0.15°C. The product in this study had a D121 of 2.0 minutes as reported on the certificate of analysis (CoA). The resistometer was programmed with a set point of 121.0°C. A series of tests were performed with the programmed set points ± 0.5°C. D-values were calculated using the Limited Holcomb Spearman Karber method. Sample replicates were 10 units and exposure intervals were less than 75% of a D-value. At 120.5°C the empirically calculated D-value was 2.3 minutes, at 121.5°C the empirically calculated D-value was 1.9 minutes. As shown above, the theoretical values are 2.2 and 1.8 minutes. However, the original product D-value calculated at 121.0°C was actually 2.038 and rounded down to 2.0 minutes, thus a slight shift upward in the empirically calculated D-values could be expected.
This demonstrates that the spores remained a reliable evaluator of the mechanical test equipment conditions. In the past, we were only too quick to blame the spores for disparate data. As indicated above, the spores remained consistent and predictable. The spores demonstrated that it was the calibrated instruments and the mechanical device that varied.
Therefore, one should conclude that if the standards allow a ± 0.5°C tolerance on the mechanical test equipment then it goes without saying that we have to expect a corresponding variance of approximately ± 10% of the D-values on the CoA.
When it comes right down to it what do ± 0.2 minutes really mean? That is a variance of ±12 seconds. The application of BIs is to monitor loaded process vessels. In contrast to resistometers, process vessels may take 10 to 20 minutes to come up to sterilizing conditions depending on the load. The temperature during the exposure phase may fluctuate by several degrees and will take substantially longer than 10 seconds to reduce the chamber temperature. The actual conditions will vary with each different load. The result is a delivery of lethality that is very different from the lethality delivered by a resistometer.
A report published by FDA (Oxborrow et. al. 1990) indicated that D-values performed in the same laboratory have a normally expected variance of ± 20% from the stated certificate value. Testing performed by second-party laboratory verification of the certificate value could be expected to have variances of ±43%.
Don’t paint yourself into a corner by establishing an unobtainable limit in your purchase specification. A D121 tolerance window of 0.4 minutes can only be achieved if all requirements are met by the standards. Any tighter tolerances exceed predictable results required by the current regulations. They may be achieved for any one lot of BIs, but to expect it time and time again is unrealistically restrictive.
SN006-V1