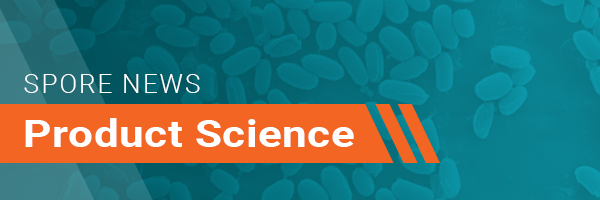
SEM Analysis of Vaporized Hydrogen Peroxide Biological Indicators
By Kurt McCauley
There is a perception by some in the industry that the performance of a vaporized hydrogen peroxide (VH2O2) biological indicator (BI) can be predicted based solely on its appearance under a Scanning Electron Microscope (SEM). In fact, some companies are leaning toward using this subjective test as a primary factor in their incoming inspection. This edition of Spore News will discuss the limitations of such an approach.
The Scanning Electron Microscope is an amazing tool, and we have spent many hours viewing spores deposited on a variety of substrates. Some of the images are so interesting that we have actually framed them…a sort of “nerd art”. But is it reasonable to assume that the performance of a BI lot can be predicted based on its appearance under the SEM?
VH2O2 is an effective anti-microbial agent, but its ability to penetrate is poor, thus restricting its effectiveness to that of a surface decontamination agent. It stands to reason that BIs used to monitor this process must be produced in a manner that readily allows VH2O2 contact with the spores. The assumption is that if a spore is protected by debris, clumping, etc., then the VH2O2 penetration is impeded leading to a positive BI (keeping in mind that it only takes one surviving spore for the BI to be positive for growth). With the SEM technology giving us the ability to find these flaws on a BI, why wouldn’t we use it?
An experiment was performed to help answer this question. Mesa Labs obtained BIs from four manufacturers, subjected them to SEM analysis, and performed resistance testing on three of the four (too few units were obtained from one lot to perform resistance testing).
Presented below are four pairs of SEM photographs taken on the BIs from each manufacturer. The right-hand photo of each set shows a monolayer, which contains the majority of the spores, covering a large surface area of each BI. The left-hand photos show spore protection by contaminating material. Surface flaws and spore piling were also present on each BI (images not presented here).
Manufacturer A: spores associated with debris (left) and spores in monolayer (right)
Manufacturer B: spores associated with debris (left) and spores in monolayer (right)
Manufacturer C: spores associated with heavy film (left) and spores in monolayer (right)
Manufacturer D: spores associated with debris (left) and spores in monolayer (right)
In our judgment, the BIs from manufacturer “D” had the best presentation of the spores on the carrier, while BIs from manufacturer “C” had the worst (spores covered by heavy film). Results from the resistance testing performed on these two BI lots proved to be the opposite of what one would expect based on the visual inspections. The BIs from manufacturer “D” showed heavy tailing (a non-linear kill curve including a high number of late positive BIs), while the BIs from manufacturer “C” showed very few survivors even at the shortest test intervals.
This testing was performed in the Apex® isolator located at Mesa’s Bozeman Manufacturing Facility. Would the results have been different if the testing had occurred in a different system? Isolator designs and operating parameters are certainly not uniform. It stands to reason that a particular category of BI imperfections may have little to no impact in some isolator systems but may be very problematic in others. Feedback from the industry seems to align with this as one client will reject a BI lot based on performance while another client will favor that same lot.
There is little argument that the ideal BI would consist of a perfect monolayer of spores deposited on a uniform, flaw-free surface, completely void of contaminating materials. An ideal BI Lot would then consist of hundreds or thousands of these BIs, which would all die in unison when subjected to a VH2O2 treatment. Of course, this is not possible, and no one is suggesting that it is.
Years of data collection in the industry have demonstrated that “hyper resistant” BIs will exist at some level in every BI lot. Using SEM analysis to gauge this level would be a monumental task. To thoroughly examine just one disc could easily take one hour, but the larger issue would be to identify the cause of the hyper resistance…and in most cases, this would purely be a subjective judgment call.
While SEM images are interesting and provide amazing detail, it is unreasonable to accept or reject a BI lot based solely on this subjective analysis. The best method to screen a BI lot is to evaluate its performance in a test isolator that operates under the same parameters as the production isolator. In doing this, the BI in its entirety is evaluated and not just one particular aspect of the BI.
We do not discourage the use of the SEM but be cautious about what you think the images are telling you.
SN051-V1