Cap Torque Testing: Standards and Regulations You Need to Know
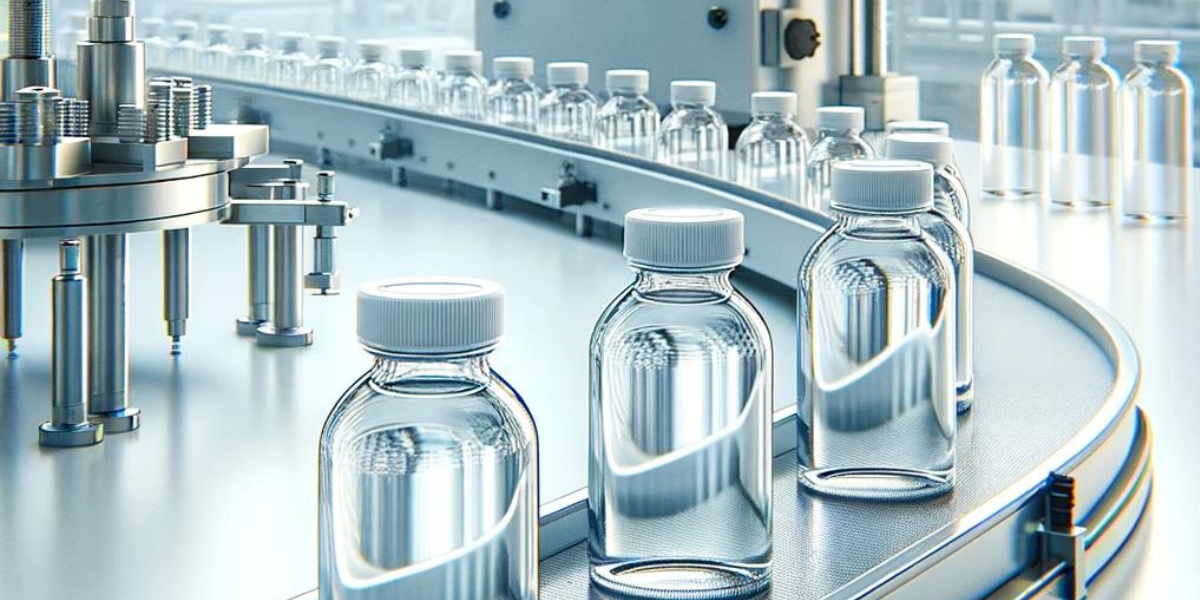
In precision-driven industries such as pharmaceuticals, chemicals, food & beverage, and cosmetics, cap torque testing is a critical component of quality control processes. To ensure seal integrity, ease of opening, potency/taste, shelf life and operator safety, it's essential for professionals in quality, packaging, manufacturing, process, and validation to be well-versed in the pertinent cap torque testing standards and regulations. In this technical article, we will delve into the key standards from ASTM, ISBT, and ISO, as well as regulations from FDA, OSHA, and EPA that shape the landscape of cap torque testing.
Understanding Cap Torque Testing
Cap torque testing measures the application and removal force of caps on containers. This process is vital for ensuring the product's integrity, safety, and compliance with various industry standards and regulations. An optimal cap torque ensures that the product is sealed correctly, preventing leaks and maintaining the product's shelf life, while also ensuring that the package can be opened by the intended user.
Standards versus Regulations: What’s the Difference?
Standards and regulations play complementary yet distinct roles in the realm of cap torque testing, shaping the framework within which industries operate to ensure safety, quality, and compliance. Standards are established by professional organizations or standards bodies, such as ASTM or ISO, and represent consensus-driven best practices that outline specifications, procedures, and guidelines for cap torque testing. These standards are voluntary, serving as benchmarks for quality and performance, aiming to ensure product consistency, safety, and customer satisfaction.
On the other hand, regulations are mandatory requirements set forth by governmental bodies, such as the FDA, OSHA, or EPA, designed to protect public health, safety, and the environment. Regulations are legally enforceable and must be adhered to by organizations to operate legally. While standards can influence the development of regulations and often provide the technical foundation for regulatory compliance, failing to follow standards may not have legal repercussions unless those standards are referenced within regulations. Together, standards and regulations ensure that cap torque testing is performed accurately and consistently, minimizing risk and enhancing the integrity of packaged products.
Key Regulations and Standards
ASTM Standards
The American Society for Testing and Materials (ASTM) provides several standards relevant to cap torque testing:
- ASTM D7860-14(2022): This a crucial standard for those involved in the packaging of child-resistant and non-child-resistant containers. It specifies test methods for measuring the torque retention of continuous thread closures using automated torque testing equipment. This standard is vital for ensuring that packages are secure yet accessible, balancing child safety with the ease of opening for adults. By adhering to this standard, manufacturers and packagers can significantly reduce the risk of product tampering and ensure compliance with safety regulations, ultimately protecting consumers and enhancing the credibility of their products.
- ASTM D3475-20: This standard classifies child-resistant packaging to ensure that products are safely secured away from children, reducing the risk of accidental ingestion or exposure to potentially harmful substances. This standard guides manufacturers in selecting the appropriate packaging solutions that meet regulatory requirements while ensuring that the packaging is still functional for adult users. For industries dealing with hazardous materials, pharmaceuticals, or household chemicals, adhering to this classification is essential for product safety and regulatory compliance, impacting packaging design and testing processes.
- ASTM D3474-23: This standard focuses on the calibration and use of torque meters in packaging applications, ensuring that these devices accurately measure the torque applied to or removed from closures. This standard is fundamental for maintaining the consistency and reliability of cap torque testing, directly affecting product integrity, shelf life, and consumer safety. Compliance with this standard helps companies avoid costly recalls and reputational damage by ensuring that their products are packaged correctly and securely.
These standards are critical for ensuring that packaging meets safety and performance requirements, particularly for child-resistant packaging.
ISBT and CETIE Standards
The International Society of Beverage Technologists (ISBT) and CETIE offers standards such as the Voluntary Standard Test Methods for Plastic Flat Top Closures, covering physical performance tests like back-off, pull-up, removal torque, and application angle. These standards help ensure that beverage caps perform reliably under various conditions.
ISO Standards
- ISO 13127: This standard provides mechanical test methods for re-closable child-resistant packaging systems, setting the global benchmark for packaging safety. This standard is essential for manufacturers aiming to market their products internationally, ensuring that packaging can be safely used by adults while preventing access by children. Adherence to ISO 13127 not only facilitates compliance with international safety regulations but also supports a company's commitment to protecting consumers, especially vulnerable populations like children.
- ISO 17025: This standard outlines the general requirements for the competence of testing and calibration laboratories, ensuring the accuracy and reliability of testing results. This standard is crucial for laboratories that perform cap torque testing, as it validates their technical competency and quality management systems. Compliance with ISO 17025 enhances customer confidence in the testing services provided, supporting regulatory compliance and quality assurance initiatives across various industries.
FDA Regulations
In the pharmaceutical and medical device industries, compliance with the U.S. Food and Drug Administration (FDA) regulations is paramount. Professionals in these industries must adhere to FDA regulations to meet stringent quality control requirements.
- 21 CFR part 820.72: Part of the FDA's Quality System Regulation, this regulation mandates the control of inspection, measuring, and test equipment. 21 CFR part 820.72 is critical for ensuring that equipment used in the manufacturing process, including cap torque analyzers, is suitable for its intended purposes and produces reliable results. For companies in the pharmaceutical and medical device industries, adhering to this regulation is vital for maintaining product quality, ensuring patient safety, and complying with FDA oversight.
- 21 CFR 211.132: This regulation requires tamper-evident packaging for over-the-counter (OTC) drug products, aiming to protect consumers from tampered products. This regulation emphasizes the importance of packaging design and testing in preventing product tampering and ensuring consumer safety. For manufacturers and packagers of OTC drug products, compliance with this regulation is crucial for market access, consumer trust, and regulatory compliance.
- 21 CFR part 11: This regulation sets forth the FDA's requirements for electronic records and electronic signatures, ensuring the integrity, confidentiality, and authenticity of electronic data. This regulation is particularly relevant for automated cap torque testing systems, as it necessitates secure data capture and storage processes. Adherence to 21 CFR part 11 is essential for pharmaceutical and medical device manufacturers, supporting compliance with FDA audits and inspections while enhancing data management practices.
- 21 CFR parts 210 and 211: Cover the good manufacturing practices (GMP) for drug products, emphasizing the importance of control in the packaging process.
OSHA Regulations
The Occupational Safety and Health Administration (OSHA) provides regulations aimed at ensuring a safe working environment. These regulations underscore the importance of implementing safety measures during cap torque testing processes to protect personnel.
- 29 CFR Part 1910.900: This regulation addresses the prevention of musculoskeletal disorders, including repetitive motion injuries, in the workplace. This regulation underscores the importance of ergonomic solutions and automated equipment in reducing the risk of injuries among operators performing repetitive tasks, such as cap torque testing. For companies, compliance with this OSHA regulation is crucial for ensuring worker safety, reducing absenteeism, and maintaining productivity.
- 29 CFR part 212: This regulation includes general machine safety requirements, focusing on safeguarding operators from potential hazards associated with the operation of machinery, such as automated cap torque testers. This regulation is essential for ensuring that machinery used in manufacturing and packaging processes is equipped with necessary safety features, such as two-hand controls to prevent accidental operation and guards to protect against pinch points and projectiles. Adherence to this regulation is critical for manufacturers, as it directly impacts the safety of the workplace, reduces the risk of occupational injuries, and ensures compliance with OSHA's safety standards. For companies utilizing automated cap torque testing equipment, incorporating these safety measures is vital for protecting operators and maintaining an efficient, compliant production environment.
US Consumer Product Safety Commission (USCPSC)
- 16 CFR part 1700: This regulation outlines the Poison Prevention Packaging Act's requirements for child-resistant packaging. This regulation mandates testing and certification processes to ensure that packaging is both child-resistant and senior-friendly. Compliance with this regulation is critical for manufacturers of potentially hazardous consumer products, ensuring that packaging designs protect children from accidental poisoning while remaining accessible to adults, directly influencing packaging testing and certification processes.
Department of Transportation (DOT) Regulations
- 49 CFR parts 173 and 178: These are key regulations under the Department of Transportation (DOT) that govern the packaging and transportation of hazardous materials. Part 173 specifies the requirements for the safe shipment of hazardous materials, including packaging, marking, labeling, and documentation. Part 178 sets forth the specifications for packaging that can be used for hazardous materials, ensuring that they are designed, constructed, and tested to meet safety standards during transportation. These regulations are crucial for manufacturers and shippers of products that contain hazardous chemicals, pharmaceuticals, or other dangerous goods. Compliance ensures the safe and legal transportation of these materials, minimizing the risk of spills, leaks, or accidents during transit. For companies involved in the production and shipping of such goods, understanding and adhering to these regulations is integral to daily operations, ensuring product safety, environmental protection, and regulatory compliance.
EPA Regulations
In industries where environmental impact is a consideration, adherence to regulations set by the Environmental Protection Agency (EPA) is crucial. While cap torque testing itself may not directly fall under EPA regulations, the materials used in closures and containers must comply with environmental standards to mitigate any adverse effects. Professionals should be aware of EPA regulations governing materials and recycling practices.
- Resource Conservation and Recovery Act (RCRA) - Title 40 CFR Parts 239 through 282: The Resource Conservation and Recovery Act (RCRA), particularly Title 40 CFR Parts 239 through 282, provides comprehensive guidelines for the management of hazardous and non-hazardous solid wastes. This regulation is relevant to companies involved in packaging, especially those dealing with hazardous materials, as it dictates the safe disposal, treatment, and storage of waste. Proper cap torque testing ensures that containers holding hazardous materials are securely sealed to prevent leaks and spills, which could lead to significant environmental damage and regulatory penalties. For quality, packaging, and manufacturing professionals, adherence to RCRA standards underscores the importance of effective cap torque testing to ensure container integrity, thereby supporting environmental protection efforts and compliance with waste management regulations.
- Clean Air Act (CAA) - Title 40 CFR Parts 50 through 99: The Clean Air Act (CAA), specifically Title 40 CFR Parts 50 through 99, aims to control air pollution by setting limits on the amount of specific pollutants that can be released into the atmosphere. While not directly related to cap torque testing, the relevance comes into play when considering the packaging and storage of volatile organic compounds (VOCs) or other airborne pollutants. Properly applied cap torque ensures that containers storing VOCs or chemicals that can emit harmful air pollutants are adequately sealed, minimizing the release of these substances into the environment. For individuals responsible for the packaging process, understanding the implications of the CAA highlights the critical role of cap torque testing in preventing air pollution and ensuring regulatory compliance, emphasizing the need for precision and reliability in packaging operations that could impact air quality.
Recent Announcements from the EU
In the area of sustainability, the European Union's Single-Use Plastics Directive (SUPD), a landmark move to curb plastic waste, mandates tethered caps on all single-use plastic beverage containers up to three liters starting July 2024. Initially met with resistance from global giants like Coca-Cola, Danone, Nestlé, and PepsiCo, the legislation aims to tackle the prevalent issue of plastic litter on European beaches by ensuring caps remain attached to bottles, reducing the chance of them becoming marine debris. Despite the industry's concerns over the significant investments required for new designs, molds, and possibly machinery, the directive was adopted swiftly, signifying a major shift towards enhancing recycling efforts and minimizing environmental impact. This move has sparked innovation within the packaging industry, as companies begin to navigate the challenges of complying with the directive while minimizing additional costs to consumers.
In response to the SUPD, the European Commission tasked the European Committee for Standardization (CEN) with developing a standard for tethered cap designs, emphasizing the need for durability, safety, and minimal impact on user experience. Various manufacturers have since explored innovative solutions, such as hinged tops and lasso closures, to meet these requirements without significantly disrupting existing production lines or increasing costs. Sacmi and Retal, for example, have developed tethered closures that align with the new standards, demonstrating the industry's ability to adapt to regulatory changes. Meanwhile, companies like Packamama are leveraging the directive to advance sustainable packaging solutions, highlighting the potential for tethered caps to not only comply with legislation but also contribute to broader environmental goals. This EU regulation is poised to set a precedent, with potential for broader adoption beyond Europe as part of a global shift towards more sustainable packaging practices.
Conclusion
Navigating the complex landscape of cap torque testing requires a deep understanding of both industry-specific standards, broader regulatory frameworks, and sustainability goals. Professionals in quality, packaging, manufacturing, process, and validation must stay informed about ASTM, ISBT, and ISO standards, as well as FDA, OSHA, and EPA regulations to ensure compliance and uphold the highest standards of product quality and safety.
By incorporating these standards and regulations into their cap torque testing processes, industries can not only meet the necessary requirements but also enhance the overall efficiency and reliability of their quality control measures. This comprehensive approach contributes to the overarching goal of producing safe, high-quality products in accordance with global standards and regulations.
Ready to Explore Further?
Explore Mesa’s portfolio for cap torque testing. As the leader in customizable solutions for caps and containers, partner with Mesa to design accurate, flexible, and heavy-duty manual and semi-automatic cap torque analyzers for laboratory and production environments in industries ranging from food and beverage to pharmaceutical and medical device.
Our automated cap torque analyzers are designed to eliminate operator variation and ensure consistency, critical for meeting the stringent requirements of ASTM, ISBT, and ISO standards, as well as FDA, OSHA, USCPSC, and DOT regulations.
- Automated Testing: Our automated solutions apply consistent forces, reducing the risk of repetitive motion injuries and ensuring ergonomic safety as outlined by OSHA and USCPSC.
- Regulatory Compliance: Equip your operations with tools that help adhere to FDA and DOT regulations, ensuring that your products meet the highest standards for safety and quality.
- Data Integrity: In line with 21 CFR part 11, our systems provide secure, accurate data capture, essential for regulatory compliance and quality control.
- Accredited Calibration: Mesa Laboratories is accredited to calibrate cap torque analyzers according to ISO 17025, ensuring the accuracy and reliability of your measurements.