VOL 10, ISSUE 2
Total Viable Spore Counts
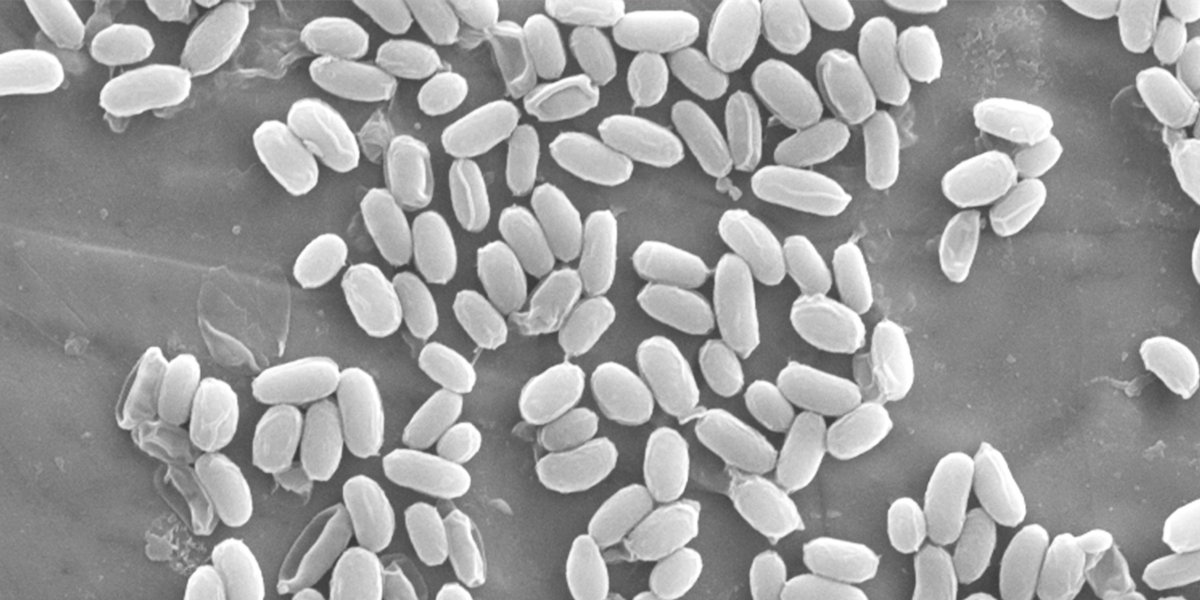
By Robert Bradley
Total viable spore count testing is a common, in-coming inspection test for biological indicator (BI) users. This test serves as one of the simpler tools that an end user can use to ensure the quality of the product they are receiving. As an end user prepares to perform this test they might ask the question ‘‘what procedure should I use?”. The answer might not be as straight forward as you would expect. There isn’t a ‘one size fits all’ answer. Both the United States Pharmacopeia (USP) and the International Organization for Sterilization (ISO) list procedures that vary from one another for determining viable spore counts and most BI manufacturers have developed procedures of their own that are specific to there product variations. So what is the right answer? Let’s look at the standards and manufacturer specific procedures first and see what we turn up.
USP <55> provides the most detailed procedure of the two standards. USP requires a minimum of three test samples. USP outlines three different procedures: paper carriers, non-paper carrier and suspensions. These three procedures only vary at the first step, eluting or removing the test organism from the test sample. For this article we will focus on the paper carrier.
- Elute the test organism from the test samples. Disperse the paper into component fibers by placing the three test specimens into a sterile 250ml cup of a suitable blender containing 100ml of chilled, sterilized purified water and blend for a time known to be adequate to achieve a homogeneous suspension.
- Transfer a 10ml aliquot to a sterile screw-capped 16 x 125mm tube.
- Heat shock the tube at the appropriate temperature
- thermophiles: 95-100°C for 15 minutes
- mesophiles: 80-85°C for 10 minutes
- Remove from heat shock and rapidly cool in an ice-water bath at 0-4°C.
- Transfer two 1ml aliquots to suitable tubes and make appropriate serial dilutions in purified water. The selected dilutions should be those that will preferably yield 30-300 colonies but no fewer than 6 on each pair of plates.
- Plate 1ml of each selected dilution into each of two Petri dishes.
- Within 20 minutes add 20ml of agar that has been melted and cooled to between 45-50°C. Allow to solidify.
- Invert the plates and incubate at the appropriate temperature for 48 hours.
ISO 11138-1 is more vague than USP, it just provides a basic outline of a procedure. ISO requires a minimum of four test samples. It states that the test samples should be placed in an appropriate volume of suspending medium and that the test organism should be eluted from the test samples by a validated procedure. Once the test organism is eluted from the samples then proceed with serial dilutions and plating in/on tryptic soy agar plates. Colony counts of 30-300 are considered the most accurate. ISO is relying on the BI manufacturers to provide the end user with the appropriate procedure for their different types of BIs.
Even though there are procedures outlined in USP you will find that a lot of BI manufacturers have validated different variations of the base procedure listed in USP. Typically this is done to increase efficiency as well as accuracy. Both the Bozeman and Omaha Manufacturing Facilities have validated variations to the USP procedure.
The Bozeman Manufacturing Facility’s procedure for paper carriers very closely follows the USP procedure with one exception:
- Maceration with glass beads rather than a blender. Instead of using a blender, the Bozeman Facility utilizes glass beads and a vortexer to macerate the paper strip:
The Omaha Manufacturing Facility has validated numerous variations to the USP procedure for paper carriers:
- 10 test samples rather than 3 test samples. This is done for two reasons; ease of use and accuracy. By using 10 samples it keeps the dilution scheme very simple. Also, using 10 test samples rather than 3 increases accuracy by giving a better average:
- 24-hour incubation rather than 48 hours: The Omaha Facility found that using their population assay procedure, purified water, tryptic soy agar and tightly controlled incubator resulted in equivalent results at 24 or 48 hours:
- Counting 10-300 colonies rather than 30-300: The Omaha Facility plates the final two dilutions, one dilution that will result in colonies counts of 100-300 and one dilution that will result in colonies counts of 10-30. By dropping the minimum count down to 10 colonies it allows the Omaha Facility to average the results from two dilutions which increases the accuracy of the result. Even though the Omaha Facility is counting colonies below the USP and ISO recommended level of 30, the counts are still above the USP minimum of 6 colonies:
The changes listed above work very well for the specific manufacturer that employs them but that doesn’t mean they should be used universally for all BIs from all manufacturers. The manufacturers produce their organisms and biological indicators using different methods. Those methods could cause the organisms they use for their BIs to react differently to a procedure that has been validated by another manufacturer. As an example, the glass bead maceration that the Bozeman facility utilizes works very well for spore strips manufactured there but if you were to utilize that method for spore strips manufactured by the Omaha facility, you will find that it won’t work as well because this facility utilizes a thicker paper which doesn’t macerate as well using glass beads.
So what is the answer? What procedure should you follow? Ideally you should use the same procedure as the manufacturer. You are trying to replicate the manufacturer’s results, the best way to do that is to follow the same procedure. Most manufacturers will gladly provide you with their standard operating procedure for performing total viable spore counts.
About the Author
Robert Bradley is the Director of Laboratory Production for Mesa Labs’ Omaha Manufacturing Facility. He started out with the company in March of 2003 as a Testing Coordinator. In that role he was involved with biological indicator production, research & development and contract studies. In 2004 he became the Laboratory Manager where he oversaw biological indicator production and contract studies. He served in that position until promotion into his current role in October of 2010.
Mr. Bradley holds a B.S. in Biology from Midland Lutheran College and a M.S. in Biology from the University of Nebraska at Omaha. He is a member of the Association for the Advancement of Medical Instrumentation (AAMI), the Parental Drug Association (PDA), and the American Society for Microbiology (ASM).